By Drew Robb
It never ceases to amaze me the extent and sophistication of facilities owned by “smaller” players in the turbomachinery world. With so much attention lavished on the likes of GE, Siemens, Baker Hughes, and Mitsubishi Power, you can begin to think that they are the only ones with large plants and sprawling campuses. Yet tour after tour of places like Elliott, Capstone Green Energy, LA Turbine, Mee Industries, and others makes it clear that all are big concerns packed full of state-of-the-art equipment. A tour of the Power Systems Mfg. (PSM) plant in Jupiter, Florida once again proved this to be true. The place is huge. And the company does far more than most people realize. It is gearing up to provide the combustors and other systems to support decarbonization initiatives.
EARLY DAYS
PSM emerged around two decades back, profiting from a decision by Pratt & Whitney to move its major military aerospace engineering group from South Florida’s east coast up to Connecticut. PSM gobbled up many skilled engineers and put them to work in the commercial power generation space. The first major release was the LEC-III combustor. It guarantees sub-5 parts-per-million (ppm) NOx emission levels when operated on natural gas over the entire premix operating range, from baseload down to 80% relative load (respectively 50%-60% with inlet bleed heat system). CO emissions under these conditions are typically measured in the low single digits. Developed for implementation in B & E-class turbines, including GE Frames 6B, 7B/EA, 9E, and Siemens/ Westinghouse 501B6/D5, it can either be a drop-in replacement for existing OEM DLN1 systems, or be part of a conversion from standard diffusion combustion systems. No changes to the control systems are needed for vintages Mark V and higher.
Almost 100 have been sold to date. Two decades later, and after multiple ownership changes (Calpine, Alstom, and Ansaldo Energia), PSM is now part of Koreaheadquartered Hanwha, a company with an emphasis on renewables, the hydrogen supply chain, and decarbonization.
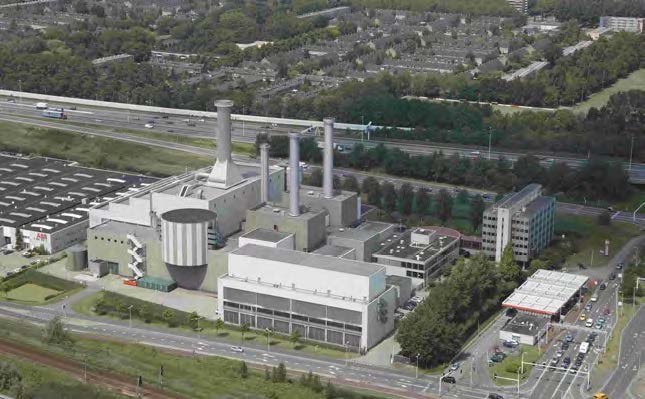
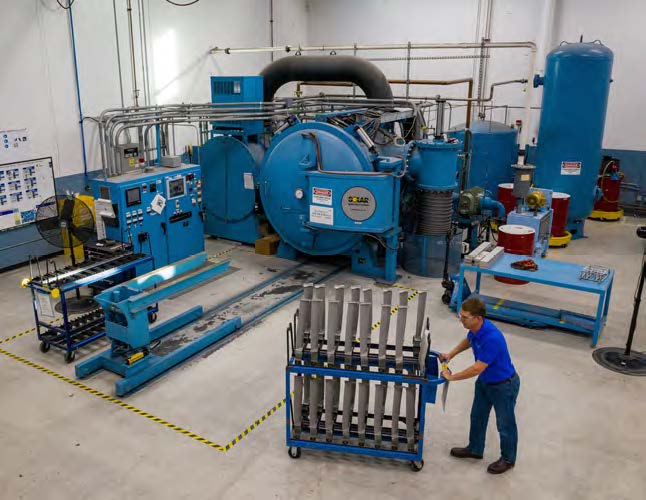
FACILITY TOUR
The front of the building houses administrative offices. At first glance, it doesn’t look that big. But it stretches back endlessly with most space given over to production lines, repair processing cells, testing, and other engineering functions. The company isn’t in the business of re-engineering a “good enough’ replacement part for existing engines. Its goal is to offer technologically advanced aftermarket gas turbine components and performance upgrades, parts reconditioning, and repairs. These are available for the Frame 6B, 7B/E/EA, 7F, 9E, 9F, and 501F transactionally or as part of a flexible long term service agreement. It supports this with local execution centers based in the US, Europe, Asia, and the Middle East.
“Our repair and upgrade capabilities can outperform OEMs on life extension and repair yields,” said Jeff Benoit, Vice President of Clean Energy Solutions at PSM.
As the tour progressed, he showed me rooms full of R&D personnel working on current projects as well as new designs. One section dealt with combustors. As well as the LEC-III, PSM has also developed the FlameSheet combustor. It employs a can-annular “combustor within a combustor” concept as well as fuel/air mixing to provide turndown to 30% of base load turbine operating load range increase while maintaining single digit NOx & CO emissions. Designed to operate up to 32,000 factored hours between maintenance intervals, it is suited to shale gas, Liquefied Natural Gas (LNG), or alternate fuel operation such as ethane, propane, and hydrogen. PSM is commercially offering this combustor platform for up to 40% hydrogen by volume. FlameSheet is often sold along with PSM’s Combustion AutoTune system that enables automated combustion tuning to maintain emissions and combustion dynamics within specified limits under varying environmental or fuel heating value conditions. Its purpose is to achieve optimal gas turbine operation from a reliability and performance standpoint.
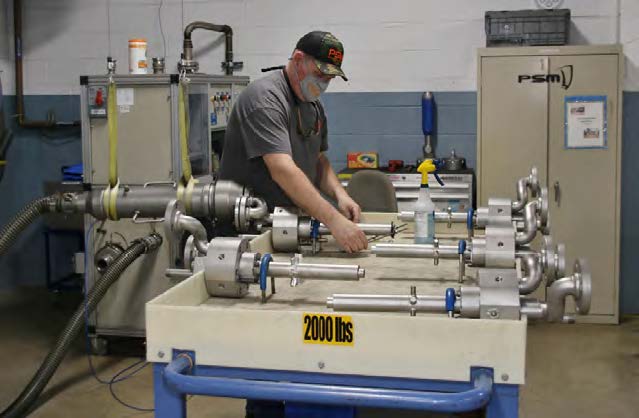
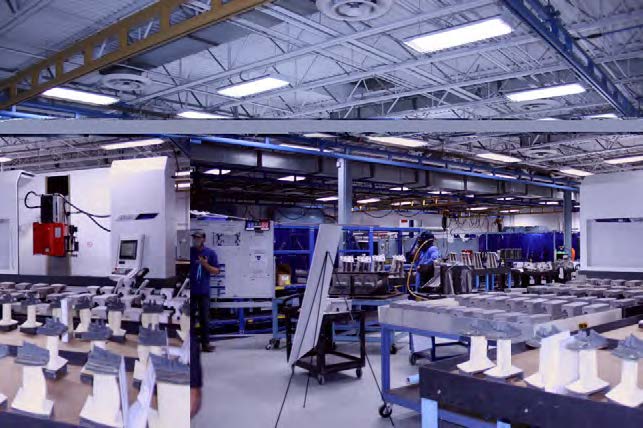
Another part of the plant dealt with rotor repair, life extension, and management. Using 3D steady state and transient analysis models, aged PSM’s HyFlex FlameSheet Combustor material properties, a portfolio of rotor and blading design upgrades, and non-destructive testing and analysis toolset, PSM can service a wide range of turbines. Rotor service capabilities include rotor removal, inspection, ship and install, with capabilities to inspect, assemble, repair and balance. An in-house team provides analysis for disk repair or replacement approaches and life evaluation/ extension, and supplies all required ownmake parts including blades, fasteners and disks, many with improvements developed by PSM.
“If a company wants to change the way its machines operate to fit shifting market conditions, we are happy to be involved as we understand the various dynamics,” said Benoit. “Some want emissions lowered, some want more power, and others want as little maintenance as possible. Regardless of needs, almost every plant has to change the way they operate to a manner that rarely fits with the original design.”
As we walked through the place, turbine and compressor parts were everywhere. Some were being cleaned, some assessed and others, repaired, enhanced, coated, or 3D printed.
An unexpected aspect of the tour was a control room conducting remote monitoring and diagnostics of many gas turbines and other rotating equipment from around the world. PSM has Long Term Service Agreements (LTSAs) in place for dozens of plants. It offers operators part life guarantees, coverage during unscheduled inspections, control of inventory, service management, reconditioning, repair, field services, monitoring & diagnostics, and engineering assessments.
HYDROGEN
PSM is hard at work servicing the existing fleet of gas turbines. But it also involved in the development of the next generation of equipment. It is investing heavily in the hydrogen space, including upgrades LEC-III and FlameSheet combustor retrofits that can installed into OEM machines to co-fire variable blends of hydrogen and natural gas, with a development road map to allow a 0 to 100% range of hydrogen without the need for water, steam or nitrogen diluents to limit emissions.
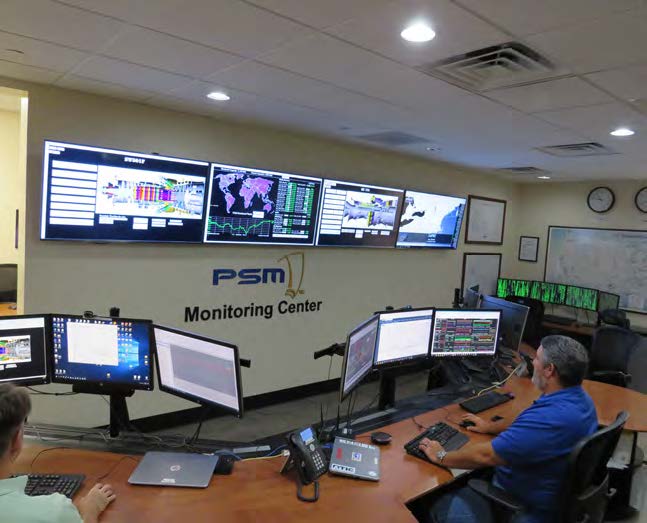
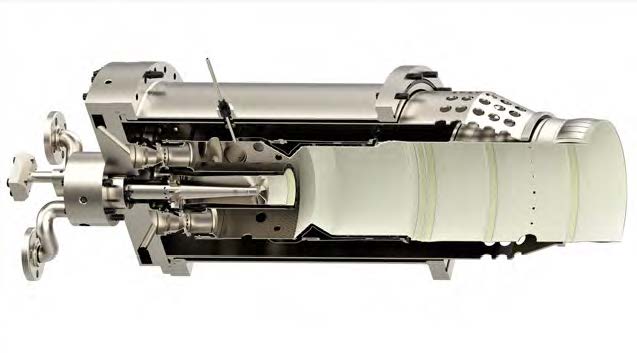
For example, a sister plant in The Netherlands run by Thomassen Energy (also part of the same division within Hanwha) is going to retrofit one of the Uniper Rotterdam Capelle (RoCa) power plant’s gas turbines with the PSM HyFlex LEC-III combustion system capable of being operated with a variable blend of hydrogen and natural gas fuel. The RoCa plant in the Zuid-Holland Province has a net electrical output of 264 MW. It has two Frame 5 gas turbines commissioned in 1983 (RoCa 1 & 2) and one Frame 9E (RoCa3), manufactured by Thomassen, commissioned in 1996.
In 2023, Uniper is planning to switch the RoCa plant’s fuel source from Groningen natural gas to a high caloric gas supply. Uniper anticipates blending the new gas supply with upwards of 30% H2 while maintaining low emissions when coupled with an AutoTune system. This retrofit system has already been operating on three Frame 9E turbines in the Netherlands at another location since 2018 with up to 25% hydrogen.
Benoit sees an immediate market for hydrogen-based combustion and gas turbine systems for dealing with refinery off gas. Regulations are tightening and flaring is gradually being eliminated as part of decarbonization objectives. Facilities, therefore, will seek a way to utilize the hydrogen refinery off gas economically. Providing it to their power and steam generation assets is one obvious option.
“Decarbonization does not mean the disappearance of the gas turbine,” said Benoit. “With so much natural gas available in the U.S., blue hydrogen (hydrogen produced from natural gas) is likely to be the most viably available bridge over to green hydrogen in the years to come.”
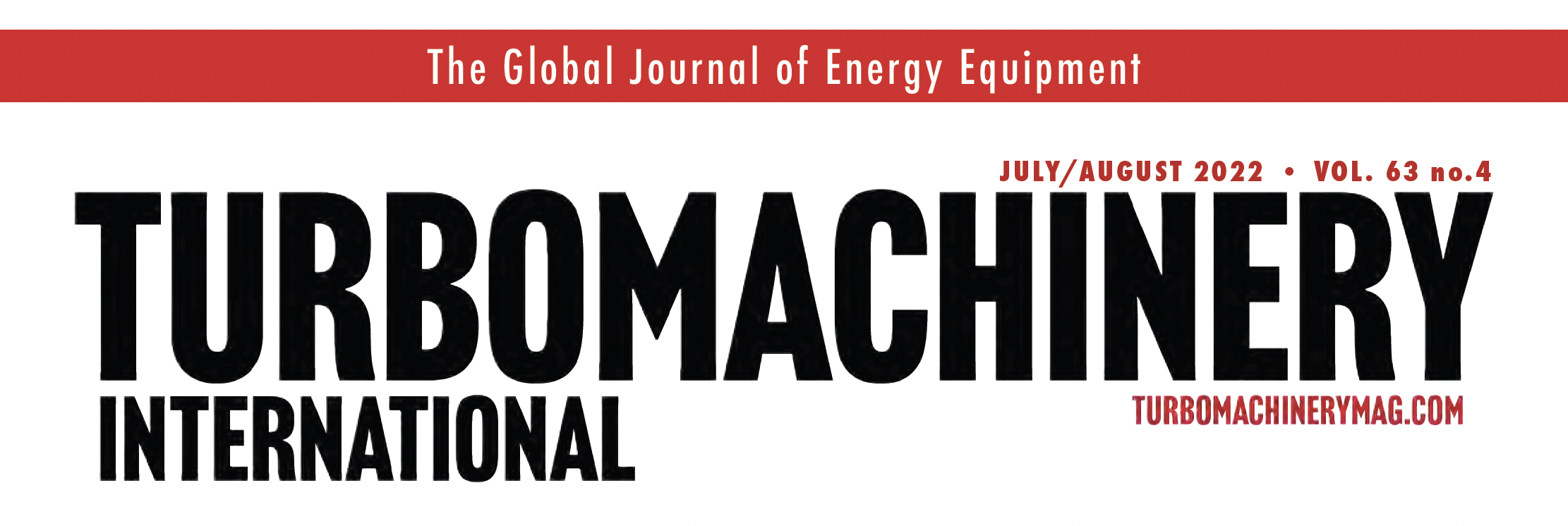
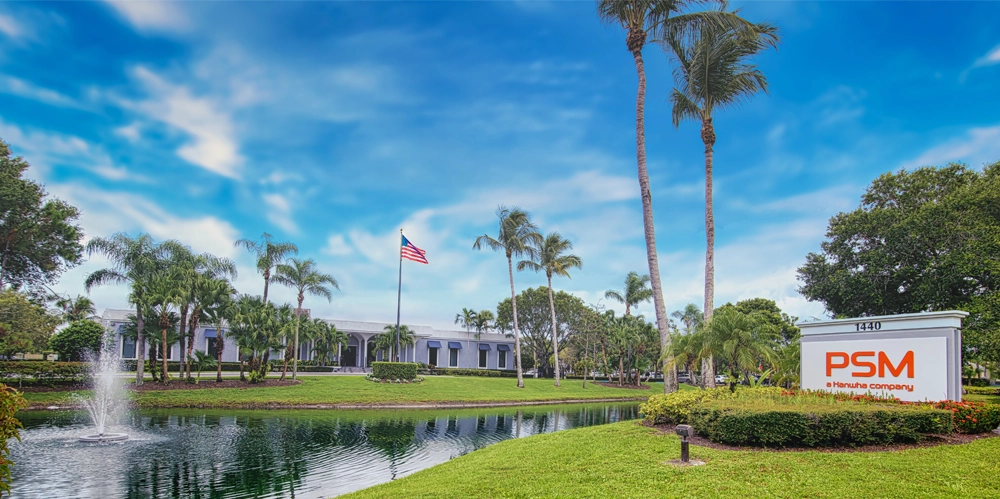